Kaizen: Continuous Improvement with the Kaizen Method
Kaizen is a management philosophy aimed at continuously improving and developing processes, products, and services. Originating from Japan, Kaizen means "change for the better" or "continuous improvement."
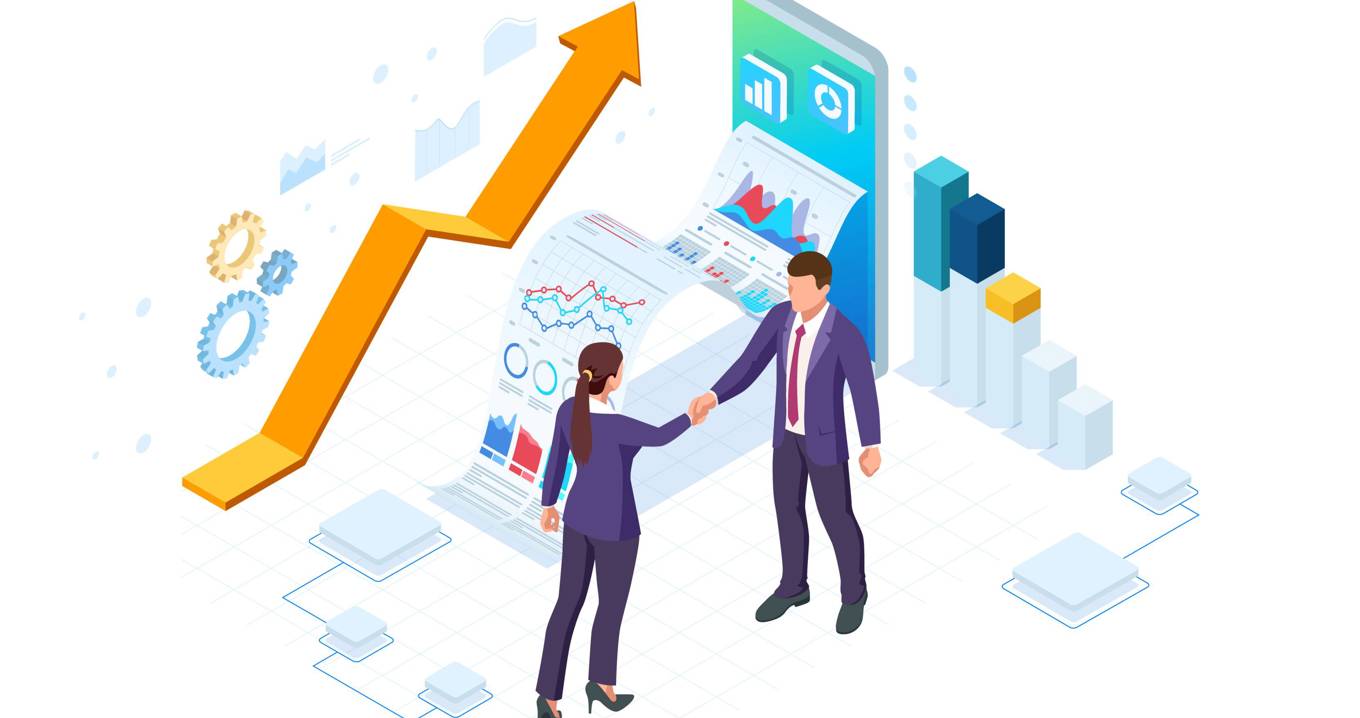
What is Kaizen?
Kaizen, commonly translated as "continuous improvement," is a Japanese management philosophy that revolutionised the country's manufacturing sector in the 1950s. The Kaizen method was coined by Taiichi Ohno, known as the "father" of Toyota's production system.
Ohno developed the Kaizen method by focusing on eliminating waste in the production process and continually improving it. This method became a vital part of Toyota's production philosophy, helping the company become the world's largest automaker.
Kaizen is an essential part of Lean Production and Six Sigma methodologies. Today, Kaizen is used in various industries and organisational types, including manufacturing, healthcare, education, and service. Kaizen has evolved into a well-established concept in leadership and Operational Management.
The Kaizen philosophy is popular because it focuses on continuous improvements that often lead to higher efficiency, productivity, and quality while minimising waste and costs.
The Kaizen Method
The Kaizen method is used for small adjustments and improvements in processes and routines daily. It is important to take small steps and make these minor improvements continuously to achieve significant improvements in the long term.
Principles of the Kaizen Method
- Continuous Improvement: The Kaizen method focuses on continuous improvement of processes and routines, building on the idea that small changes continuously accumulate to significant results in the long term.
- Teamwork: In the Kaizen method, it's crucial to involve the entire organisation in the improvement process. Collaborating and sharing ideas can create innovative solutions that benefit the entire organisation.
- Ongoing Training and Development: Since the Kaizen method is based on continuous improvements, it involves continuously training and developing staff to increase their competence and ability to contribute to the improvement process.
- Standardisation: An important part of the Kaizen method is standardised processes and routines to achieve efficiency and quality in work.
- Visualisation: Documentation and visualisations are used to make processes and improvements visible to everyone in the organisation. This can include the use of charts, graphs, and other tools to show progress and results.
By using the Kaizen method, you can gain many benefits, such as increased productivity, improved quality, and increased efficiency. This is because small daily improvements can add up to significant improvements over time.
Implementing the Kaizen Method
Implementing the Kaizen method in an organisation can seem overwhelming initially, but it does not have to be difficult.
6 Steps to Get Started with the Kaizen Method
1. Identify Areas for Improvement: The first step aims to find the area that needs improvement, such as a process, product, or service.
2. Map the Process and Set Goals: The next step is to map the process and set goals for improvement.
3. Analyse Data and Identify Causes of Problems: The third step involves analysing data to find the causes of problems or inefficiencies.
4. Generate Ideas for Improvements and Choose One to Implement: Based on the data analysis, generate improvement ideas, then select one to implement.
5. Implement the Improvement and Evaluate: The fifth step involves implementing the improvements and collecting data to evaluate their effectiveness.
6. Continue Making Small Improvements and Adjustments Continuously: Finally, it's important to continue making small improvements and adjustments daily.
It's essential to remember that the Kaizen method is based on small daily improvements and adjustments. According to Kaizen, by making continuous small improvements and adjustments, a culture of continuous improvement can be created, continually improving performance.
Examples of Kaizen Use
Kaizen has various applications across industries, here are some examples:
Kaizen in Manufacturing
Kaizen is widely used in manufacturing to improve production processes and reduce waste. An example could be reducing the time it takes to change tools on a machine.
Kaizen in Municipal Operations
Kaizen is used in municipalities to continuously improve the quality of municipal services. For example, in services for people with disabilities, Kaizen can improve the quality of support and service.
Kaizen in Real Estate
In real estate, Kaizen is used to continuously improve property management quality, such as improving energy efficiency in buildings.
Kaizen in the Service Industry
Kaizen can be used in the service industry to improve customer experience, such as improving response times in customer service.
Criticism of Kaizen
Like any system or method, Kaizen has both advantages and disadvantages. Critics argue that Kaizen focuses too much on short-term solutions rather than addressing fundamental issues that may require more comprehensive changes.
Additionally, implementing Kaizen in organisations with existing management systems can be challenging, and people's resistance to change can hinder the introduction and execution of Kaizen.
In conclusion, the Kaizen method emphasises the importance of continuous improvement and encourages people to set small, achievable goals. This helps create and support a culture of continuous improvement and innovation.
7-minutes video demo of Hypergenes solution: