Quality Management and Quality Management Systems
Quality Management involves ensuring quality through the right processes to handle deviations, reduce customer dissatisfaction, and meet expectations. Systematic quality work involves systematically improving what the organisation does by managing, leading, and developing in the right way.
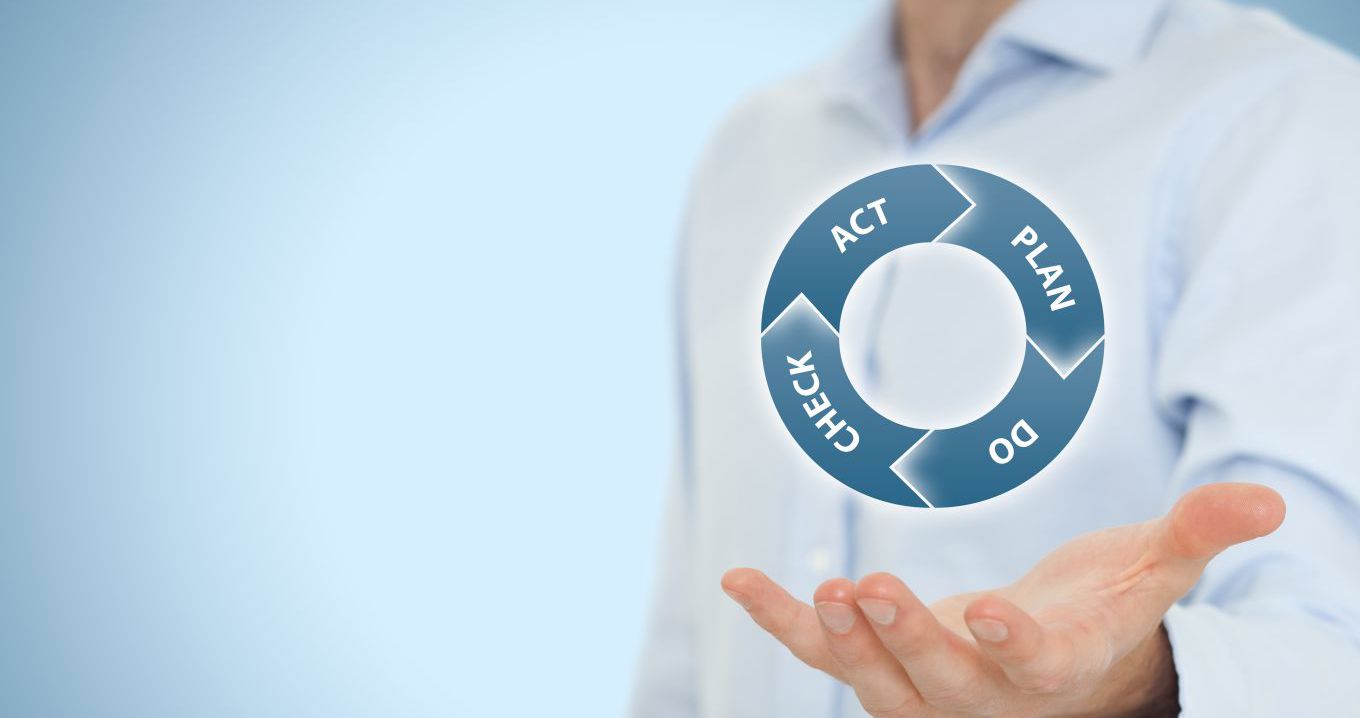
The systematic approach to quality work is the core of Quality Management, which involves continuously and structurally working to improve the quality of what you do. By its nature, it is a process and not a project that is limited in time.
The Quality Management system is a tool and a template that you use to improve the quality of the entire organisation through your quality management work.
The system involves digitising processes, creating forms to promote learning, continuous risk analysis, developing self-control models, follow-up, developing analysis material, and supporting internal control work. All with the aim of better leading, planning, controlling, following up, evaluating, and improving the business.
Internationally, 'Plan', 'Do', 'Check', and 'Act' and Total Quality Management (TQM) are talked about, based on the theories of statistician and Quality Management father W. Edwards Deming. Deming assisted in Japan during the post-war period, where awareness of statistics and Quality Management increased in manufacturing and among engineers with the help of Deming and the 'Deming Cycle'.
See the Deming Cycle and systematic quality work as a wheel (for example, an annual wheel) or a "feedback loop," where the goal is continuous improvement.
The Cornerstones of the Quality Management System
Quality in the process: Define the processes required to achieve the organisation's goals. Improve and review the processes, both because new people come into your organisation and because the requirements of the outside world and your business change. Keep a strict eye on your key processes, priorities, anchoring, and training levels.
Quality in leadership: Ensure that management is aware of resources, goals, and control of operations. Through systematic Quality Management work, management gains even better control over all the activities the business performs and can ensure that they are heading in the right direction.
Remember that leaders lead the way into new processes. They are carriers of quality and quality work culture. Employees should feel secure enough to raise concerns when things go wrong and feel confident enough to suggest improvements.
Quality in culture: Higher product quality is often enjoyed in organisations with clearly designated quality responsibility and quality-assured processes. Quality should be part of the corporate culture. Conversely, systematic improvement work can make it easier to bring up improvement suggestions and reach goals, which in itself has a positive impact on the corporate culture.
Quality in communication: Communication is important but can also be difficult. For example, in terms of Quality Management, communication can be perceived as interfering with employees' workday or involving messages that aim to change their working methods and processes.
Demonstrate results by comparing with previous years, after a year of quality work, and explain that the documentation of quality work itself is a victory; for example, in the form of a baseline analysis and Information Management.
Quality Management System and ISO
The templates in systematic quality work can involve ISO standards or procedures and can be seen as process frameworks. These are often referred to as "quality management systems". There is a clear link to the ISO 9001 standard, which is considered by many to be synonymous with systematic quality work.
ISO is a standard and certification issued by the International Organization for Standardization and is a quality mark for your quality work. There are other ways to demonstrate that your business is working with quality, but ISO certification is both common and recognised worldwide.
Those who obtain an ISO certification are often interested in demonstrating that they work with quality in a competent manner for customers or other stakeholders.
The concept of Quality Management Systems is sometimes misunderstood as software for quality management. But regardless of meaning, there are significant benefits to thinking in terms of both process frameworks and system support.
System support for quality management helps you with:
- Clear structures
- Digitised processes
- Continuous risk analysis
- Forms for promoting a learning organisation
- Models for self-monitoring
- Support in developing analysis materials
- Support in documentation
If you choose to create your own Quality Management System, it's a good idea to start with the template that best suits your needs. It's easier to have a framework to start from, which you can then rebuild and refine.
For those who don't want to use Word and Excel to manage their quality management, Hypergene's software provides decision-making support by collecting and presenting data from the business for management, managers, and those who need to keep track of Quality Management.
7-minutes video demo of Hypergenes solution: